In accordance with EU Directive 2002/96/EC of the European Parliament and the EU Council on Waste Electrical and Electronic Equipment (WEEE) and the new version of the EU Directive, 2012/19/EU, there is an obligation to collect waste electrical and electronic equipment, treat it in accordance with regulations, dispose of it and finance this. According to the German Electrical and Electronic Equipment Act (ElektroG), every manufacturer is obliged to provide a reasonable opportunity for the return of old equipment from users other than private households.
InoNet Computer GmbH takes responsibility for its products and sends them to a high-quality recycling process after use. For devices that have been used commercially or in public facilities – so-called B2B devices – we have provided convenient return and disposal solutions for you.
InoNet Computer GmbH recycles the devices it places on the market at its Taufkirchen plant. In order to be able to offer our customers the preparation for reuse, recycling and recovery of waste electrical and electronic equipment, a return shipment must be registered in advance with InoNet Computer GmbH via the following e-mail address: service@inonet.com. InoNet Computer GmbH covers the costs for the processing, recycling and recovery of InoNet Computer GmbH products. In return, InoNet Computer GmbH asks its customers to bear the costs for transportation to the recycling company, i.e. to us.
Option to return and dispose of old devices
You would like to professionally recycle an electrical appliance purchased from InoNet Computer GmbH. You have the option of commissioning a transport company of your choice or a suitable parcel service at your expense and returning the old electrical appliances to us for recycling. Personal data on the devices to be recycled must be deleted by you beforehand.
Please inform us of the quantity and device information by email (service@inonet.com) before returning the devices so that we can correctly allocate the return to recycling. You will receive a return authorization number (RMA number) from us. For this we require sender details (your data) and other information necessary for processing, see below. Please print out this information and place the printout clearly visible in the shipping container with the waste electrical and electronic equipment.
Personal responsibility with regard to the deletion of personal data
We expressly point out that in accordance with § 19a ElektroG, any personal data on the appliances to be disposed of must be deleted by you.
Meaning of the symbol for labeling electrical appliances
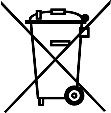
The crossed-out wheeled garbage can symbol on electrical appliances indicates that old electrical appliances must be collected separately and that they must not be disposed of with household waste.
Note: Shipping is carried out by the customer himself and at his own expense. The customer must comply with the applicable laws when shipping goods. Please observe the generally applicable shipping regulations for electrical / electronic devices and batteries.
Simplified procedure:
- Please request an RMA number from InoNet for the recycling of electronic devices
- Print out the return form (label)
- Consider shipping instructions
- Pack the old appliance in a box
- Attach the delivery bill (label) to the box
- Handover to a logistics company